Exploring the Diverse Types of Mining Industry: Above Ground, Underground, and Services and Maintenance
The mining industry has long been a keystone of global economic development, with Australia leading the way as a powerhouse of extraction, refinement, and export. Trade.gov details the Australian mining sector as a cornerstone of the economy, contributing approximately 13.6% to the nation’s GDP in 2023. Many wonder about the importance of mining in Australia and how big the mining industry is – with nearly fourteen percent of the nations GDP, it’s a big slice of the pie. The ‘Lucky Country’ has been blessed with many key minerals and is a global producer of:
- Lithium: World’s largest producer.
- Gold, Iron Ore, Lead, Zinc, Nickel: Among the top five producers globally.
- Uranium: Holds the world’s largest resources.
- Black Coal: Possesses the fourth largest resource worldwide.
Geographically, mining activities are concentrated in:
- Western Australia (WA): Approximately one-third of operating mine sites.
- Queensland (QLD): About one-quarter.
- New South Wales (NSW): Roughly one-fifth.
By volume, the most significant mineral commodities are:
- Iron Ore: 29 mines, with 97% of production in WA.
- Coal: Over 90 mines, primarily located in QLD and NSW.
This article explores the diverse mining world, encompassing the various methods used to extract resources and the critical services and maintenance operations that ensure the sector runs efficiently and safely. By understanding these facets, safety officers and engineers on site can enhance their operations, ensuring safety and productivity.
At the end of the document, we’ll go into further detail regarding SafeSmart Access’ role in protecting crews on-site with our range of solutions.
Understanding the Different Types of Mining
The mining industry holds a vital role, not only as the source of metals and minerals but as a backbone for a wide range of sectors—construction, manufacturing, technology, and even pharmaceuticals all rely on its output. Beyond driving GDP growth for producing nations, mining spurs employment and regional development, while also prompting advancements in engineering and environmental science.
By providing essential raw materials like coal, iron ore, copper, and precious metals, mining sustains the infrastructure and operational needs of countless industries. From consumer electronics to automotive manufacturing and crucial construction materials, these sectors depend on the reliable supply of resources from mining, highlighting the industry’s extensive and significant impact.
The Four Mining Types
Mining is broadly categorised into two main types based on the extraction process: surface (above ground) and underground, each with its own engineering, environmental, and economic implications. These types can be further divided into distinct operations:
- Surface Mining: Extracts minerals near the surface by removing overburden. Techniques include strip mining, open-pit mining, mountaintop removal, and dredging.
- Underground Mining: Accesses deep ore deposits via tunnels or shafts. Methods include room and pillar, narrow vein stoping, and block caving.
- Placer Mining: Uses water to separate dense minerals like gold from sediment in placer deposits, often through panning.
- In-Situ Mining: Dissolves minerals in place for extraction, commonly used for uranium and potash.
In this article, we’ll be focusing on the big two, above and underground mining.
Above Ground Mining
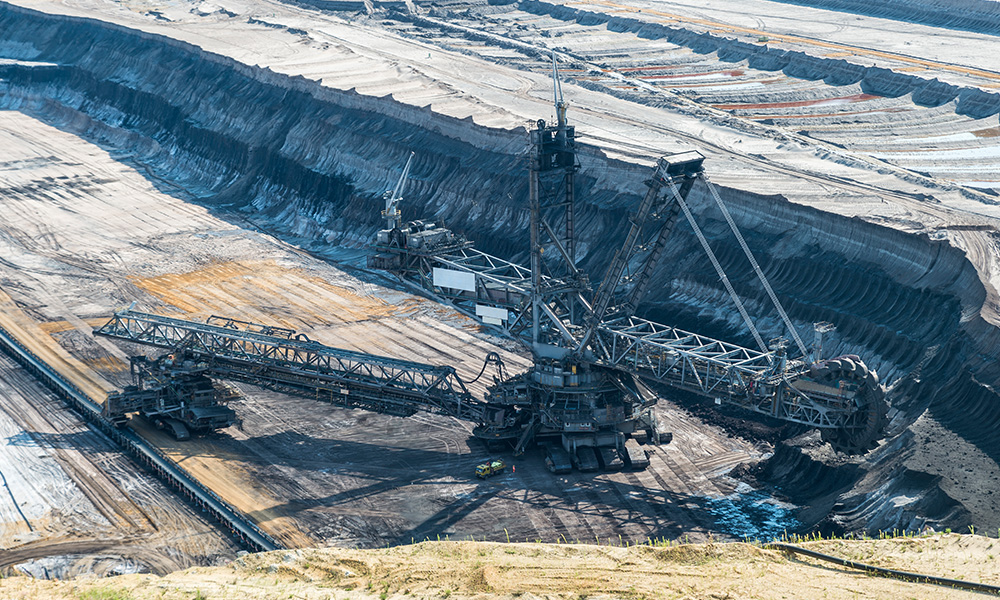
Above ground mining, commonly known as surface mining, involves the removal of overburden—layers of soil and rock lying above the mineral deposits—to access valuable resources. This method is widely used to extract materials such as coal, iron ore, bauxite, copper, and limestone.
Surface mining is favoured for its high recovery rate and relatively lower production costs compared to underground techniques, making it especially suitable for large, shallow ore deposits.
Techniques and Processes Used
- Open Pit Mining:
- Open pit mining, or open cut mining, is a large-scale excavation technique where a massive pit is created by removing overburden in a step-like manner. Miners work downwards, layer by layer, using heavy machinery to dig out ore while ensuring the stability of the pit walls. This method is ideal for near-surface, thick deposits and is commonly used for copper, iron ore, and gold. This form of mining is common in Western Australia.
- Strip Mining:
- Strip mining is used to access horizontally distributed mineral layers close to the surface. This method involves removing strips of overburden to uncover ore, which is then extracted, and the process is repeated in adjacent strips. It’s widely used for coal mining in relatively flat areas and enables efficient removal of large quantities of material.
- Mountaintop Removal Mining:
- Primarily used in coal mining, mountaintop removal involves blasting the tops of mountains to access underlying coal seams. This method reshapes landscapes, creating flat or rolling landforms post-mining, but is often controversial due to its environmental impact. It employs explosives, draglines, loaders, and haul trucks to extract coal in steep or mountainous regions.
Machinery and Equipment
Surface mining relies on heavy machinery, including crawler bucket excavators for digging, haul trucks for transporting materials, bulldozers and graders for levelling, and loaders for shifting extracted minerals. In some operations, blasting techniques are also used to break up rock layers more efficiently, often involving a series of boring machines to place explosives like ‘ANFO‘ (ammonium nitrate/fuel oil).
Each technique is carefully adapted to the specific mineral deposits, environmental conditions, and production demands, optimising the extraction process while addressing the safety and environmental challenges unique to surface mining.
Underground Mining
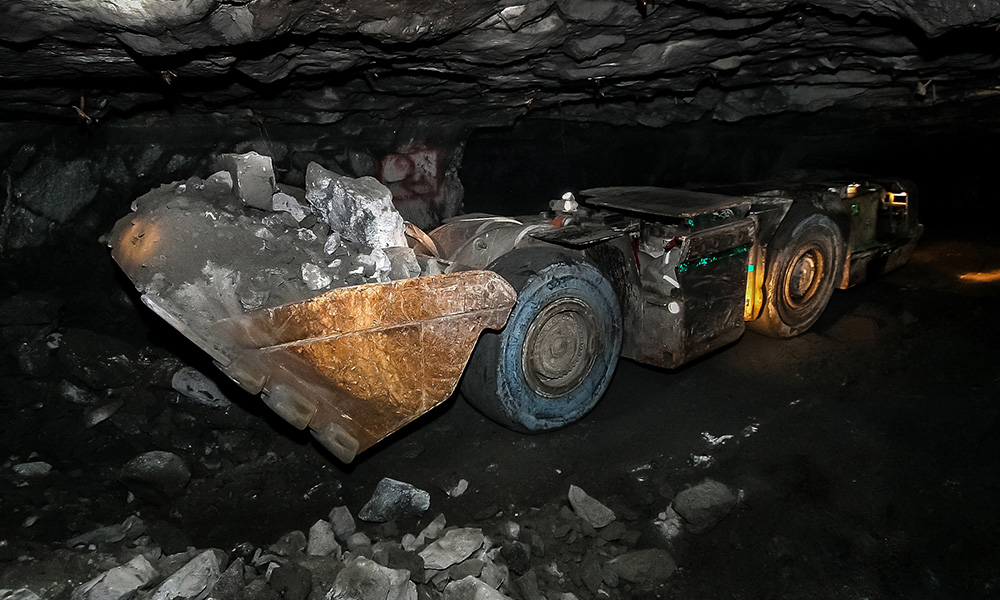
Underground mining entails the creation of subsurface tunnels (headings) and shafts to access deeply buried mineral deposits. This process is often more hazardous and costly compared to surface mining but is indispensable for extracting precious metals and minerals positioned deep beneath the earth’s surface.
Methods and Challenges of Underground Mining
Various methods are employed for underground mining, including:
- Drilling, blasting, and mucking out – Often using underground tunnels, charges are placed above the material, and the blasted material falls to a lower tunnel for removal, a process known as “mucking out.”
- Stoping (pronounced “stoap-ing”) – In stoping, miners dig out valuable ore from underground, leaving open spaces called “stopes.” These spaces can be left open or filled with stabilised materials (like waste rock or sand) to support the mine structure and prevent collapses.
- Longwall mining – A cutting machine slices coal from a long wall, while an Armored Face Conveyor (AFC) moves the coal away. Hydraulic supports protect the roof as mining progresses, allowing controlled collapse behind the work area and enabling efficient and safe coal extraction.
Each of these methods describes only the excavation process. Transporting material for further processing involves using conveyors, elevators, or vehicles to manually load and move the material.
Challenges in underground mining include technical difficulties such as equipment breakdowns, high operational costs, and significant safety risks related to collapses and gas exposure, all of which demand rigorous safety protocols.
Underwater Mining Methods
Underwater mining methods, such as dredging and seafloor mining, are employed to extract resources like sand, gravel, diamonds, and polymetallic nodules from beneath bodies of water. Dredging typically involves suctioning sediment from the seabed, mainly in shallower areas, while deeper-water techniques use remotely operated vehicles (ROVs) equipped with cutting and suction tools to collect materials.
This specialised mining technology is designed to tackle challenges like high pressure, darkness, and cold temperatures, but must also carefully manage environmental impacts, such as sediment disturbance, to protect marine ecosystems. Underwater mining plays a critical role in providing minerals essential to industries like electronics and renewable energy.
Open Cast Mining to Underground Stoping Methods
Open cast mining to underground stoping methods employ techniques like sub-level stoping, room and pillar, and block caving, each tailored to specific geological conditions. Sub-level stoping involves controlled blasting within steep ore bodies; room and pillar leaves support pillars intact within flat deposits; and block caving allows ore to collapse naturally, facilitating cost-effective bulk mining. Each of these methods optimises resource extraction as mines transition from open-pit to underground operations.
The Role of Services and Maintenance in the Australian Mining Industry
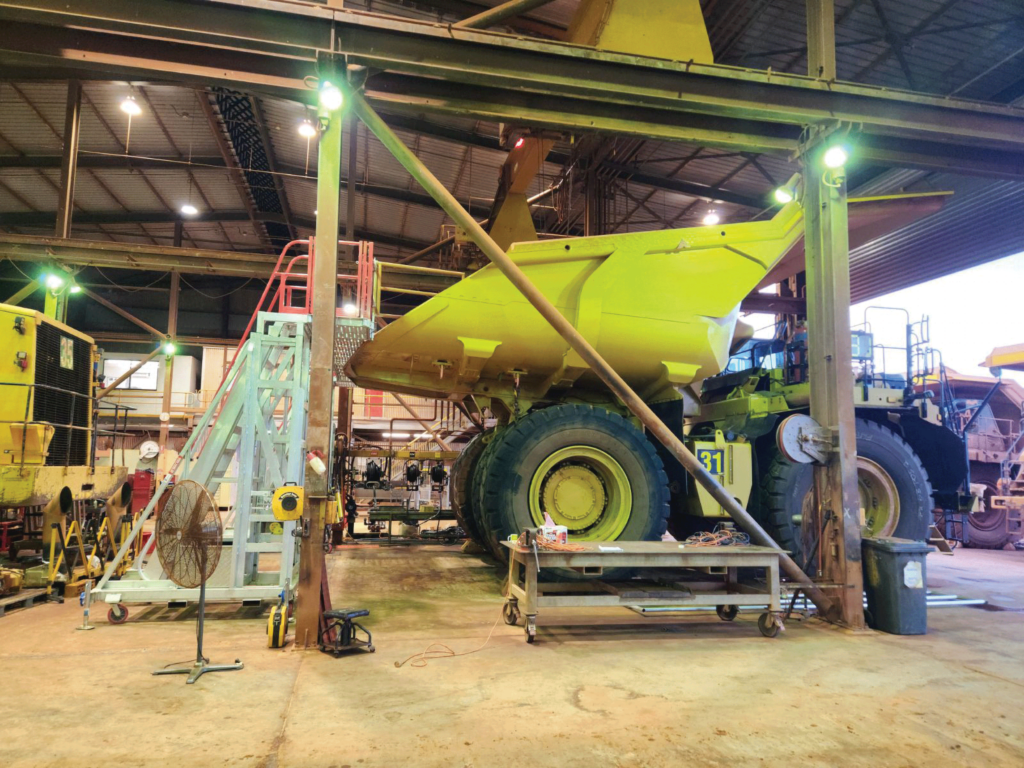
Services and maintenance are the lifeblood of the Australian mining industry, ensuring all machinery and systems run smoothly, safely, and efficiently. Given the scale and complexity of mining operations, maintenance isn’t merely a routine task but a strategic enabler that maximises uptime extends equipment lifespan and boosts overall productivity.
Most maintenance at mine sites, referred to as “shutdowns” here in Australia, is meticulously planned years in advance. These are typically brief periods of downtime during which essential upgrades and repairs are carried out. On the other hand, emergency and unplanned maintenance can be far more time-consuming, depending on the issue—whether it’s a collapse, gas exposure, part shortages, custom fabrication needs, or critical infrastructure failure.
Importance of Services and Maintenance in Mining
During mining operations, equipment reliability and performance are paramount. Regular services and maintenance help:
- Prevent Equipment Failures: Through predictive and preventive maintenance practices, potential issues are identified and addressed before they lead to costly downtimes. This systematic approach ensures that operations are rarely interrupted by unexpected equipment failures.
- Ensure Compliance with Safety Standards: Routine checks and services ensure that all machinery complies with the stringent safety regulations governing the mining industry. This compliance is critical in preventing accidents and safeguarding workers.
- Optimise Operational Efficiency: Well-maintained equipment runs more efficiently, consuming less energy and reducing waste, which in turn lowers operational costs and enhances environmental sustainability.
- Manage Costs: By reducing the frequency and severity of machine downtime, maintenance plays a crucial role in controlling operational expenditure. This proactive management of resources leads to significant long-term savings.
Types of Vehicles Used
Mining operations deploy a range of vehicles tailored to manage harsh environmental conditions and demanding workloads.
- Excavation-type vehicles: Bucket wheel excavators, surface miners, and dragline excavators are just a few of the “big boys” on-site excavating overburden and ore.
- Haul Trucks: Used primarily in surface mining, these trucks transport extracted ore and waste material over large distances.
- Loaders and Excavators: Essential for loading ore and debris onto transport vehicles, their versatility in both surface and underground mining makes them invaluable.
- Utility Vehicles: Smaller in scale, they provide flexible transportation solutions for equipment and personnel within mining sites.
Types of Bulk Material Handling Equipment Used
Equipment used to handle bulk materials in mining must be robust and efficient, ensuring quick and safe transportation of minerals:
- Conveyors: Systems that move bulk material efficiently across the mine site. Maintenance involves regular inspection of belts and mechanical components to prevent breakages.
- Hoppers and Crushers: Facilitate the initial stage of material processing, reducing large chunks to manageable sizes. They require regular servicing to prevent blockages and maintain throughput rates.
The functionality of this equipment is vital for maintaining productivity levels, and its reliability directly affects operational efficiency.
Workshop and Plant Repair Challenges
Mining equipment maintenance is critical to ensuring continuous operations and minimising downtime. Mining vehicles and bulk material handling equipment face extreme wear and tear due to harsh working conditions, abrasive materials, and constant usage. Here are some common challenges and approaches in maintaining mining equipment:
- Frequent Wear and Component Degradation:
- Heavy machinery like excavators, haul trucks, and loaders experience constant exposure to abrasive materials, which wear down components like buckets, tyres, tracks, and hydraulics. This requires frequent replacement of high-wear parts and preventative maintenance.
- To address this, maintenance teams often set up regular inspection schedules and use durable, wear-resistant materials to extend component life.
- Hydraulic System Failures:
- Many mining machines rely on hydraulic systems to power their functions, but these systems can be prone to leaks, contamination, and wear. In mining, hydraulic systems are subject to high-pressure and dusty environments, increasing the risk of contamination.
- Regular hydraulic fluid monitoring, filter changes, and sealing replacements are necessary to prevent unexpected failures and extend system life.
- Electrical and Electronic Malfunctions:
- Mining vehicles and handling equipment rely on complex electrical systems for control, navigation, and communication. Dust, moisture, and vibration can cause issues with sensors, control panels, and wiring, leading to malfunctions.
- Maintenance teams perform routine diagnostics and protective sealing on electrical components, and they often store spare parts for rapid replacement to minimise downtime.
- Structural Fatigue and Cracking:
- Mining equipment frames and structures endure heavy loads and impact, which can lead to cracks and structural fatigue over time. Detecting structural damage early is crucial to prevent catastrophic failures.
- Non-destructive testing (NDT) methods, like ultrasound and magnetic particle inspections, are commonly used to detect early signs of fatigue and cracking, allowing repairs before major issues arise.
- Conveyor Belt and Crusher Maintenance:
- Conveyors, crushers, and hoppers are essential for transporting and processing materials. However, they are prone to issues like belt misalignment, mechanical wear, and material blockages.
- Maintenance for conveyors includes belt alignment checks, roller inspections, and lubrication of moving parts. Crushers require frequent clearing of blockages and monitoring of wear on liners and jaw plates to ensure smooth processing.
- On-Site Repair Logistics:
- Mining sites are often remote, making access to spare parts and skilled technicians a challenge. Many operations set up on-site repair workshops to manage minor repairs, while more complex repairs may require specialised equipment or off-site servicing.
- Inventory management for spare parts is crucial, as is having skilled mechanics and technicians who can troubleshoot and fix issues on-site to reduce equipment downtime.
Ensuring Safety and Efficiency in Australian Mining Operations
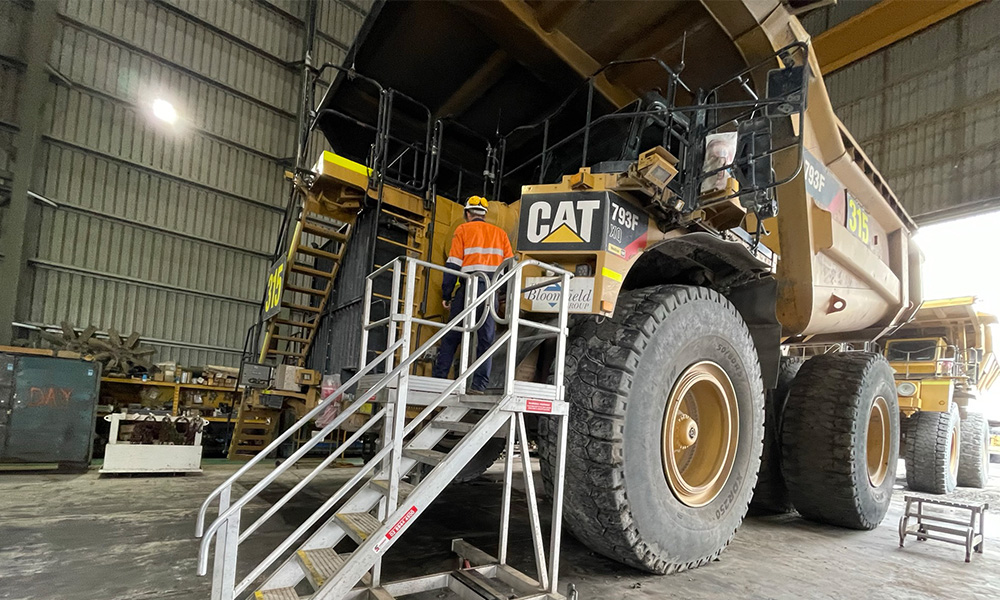
Australia’s commitment to mining safety has resulted in one of the most successful track records globally. This success stems from:
- Legislative Frameworks: Robust regulatory bodies enforce strict safety laws.
- Industry Initiatives: Companies have embraced safety as a core value, fostering a culture of responsibility and vigilance among workers.
Australian mining safety success serves as a benchmark for global best practices, demonstrating the effectiveness of continuous improvement and technological integration.
Key Mining Safety Legislation
- Work Health and Safety (WHS) Act 2011 (Federal):
- Provides a framework for protecting the health, safety, and welfare of workers across all industries, including mining.
- Enforces responsibilities for employers and workers, including risk assessment, safety training, and hazard management.
- Mines Safety and Inspection Act 1994 (Western Australia):
- Mandates safety standards specific to Western Australia’s mining industry.
- Requires regular safety inspections, risk management, and reporting of accidents and incidents in mines.
- Coal Mining Safety and Health Act 1999 (Queensland):
- Establishes health and safety protocols specifically for coal mines in Queensland.
- Includes provisions for mine safety inspections, risk management, and the appointment of safety officers.
- Mining Act 1978 (New South Wales):
- Outlines health and safety standards for mines in New South Wales, focusing on hazard control, emergency management, and worker protection.
- Requires regular safety assessments and mine site inspections.
Industry Initiatives and Programs
- Zero Harm Programs:
- Many mining companies, such as BHP and Rio Tinto, have adopted “Zero Harm” programs, emphasising no harm to workers or the environment.
- Includes regular safety training, enhanced reporting mechanisms, and incentives for safety compliance.
- International Mine Health & Safety Conference:
- A national initiative that brings together industry professionals, researchers, policymakers, and stakeholders to review and improve safety practices and share lessons learned from incidents.
- Hosts annual safety conferences to foster knowledge-sharing and encourage technological innovations in mine safety.
- Safety Reset (Queensland):
- A state-wide initiative requiring all Queensland mine workers to pause and engage in mandatory safety sessions focused on high-risk areas.
- This safety “reset” is designed to re-emphasise safety protocols, particularly after significant incidents.
Safety measures in underground mining
Underground mining is a demanding and often high-risk occupation, involving harsh conditions, confined spaces, and proximity to heavy machinery. With the constant potential for hazards like toxic gas buildup, rockfalls, and equipment malfunctions, ensuring safety is paramount. Thanks to technological advancements and rigorous safety protocols, underground mining today is safer than ever. Here’s a look at some of the critical safety measures in place to protect workers in these challenging environments.
1. Ventilation Systems: Providing Clean and Safe Airflow
One of the primary concerns in underground mining is maintaining air quality. Toxic gases such as carbon monoxide, methane, and other contaminants can accumulate quickly, putting miners at serious risk. Modern ventilation systems play a vital role in ensuring that fresh air flows continuously throughout the mine, diluting and removing hazardous gases.
Many mines today are equipped with ventilation-on-demand (VOD) systems that adjust airflow based on the number of workers and equipment in specific sections of the mine. This dynamic ventilation approach not only improves air quality but also conserves energy, allowing mines to reduce operational costs while keeping workers safe. Additionally, continuous monitoring of air quality through sensors alerts workers immediately if there is an increase in harmful gas levels, enabling swift evacuations when necessary.
2. Structural Supports: Reinforcing Tunnels to Prevent Collapses
Mining involves creating extensive networks of tunnels and chambers within the earth, and without proper reinforcement, these structures are prone to collapses and rockfalls. Various structural support methods are employed to stabilise these spaces, ensuring that workers can move and work safely.
Commonly used structural support techniques include rock bolting, where long steel rods anchor layers of rock together, and shotcrete, a sprayed concrete coating that reinforces the tunnel walls. Some mines also use wire mesh and advanced monitoring systems that detect shifts or vibrations in the rock, which might indicate a weakening structure. With these supports in place, miners can work in stable, secure environments, reducing the likelihood of catastrophic incidents.
3. Gas Monitoring and Detection Systems: Staying Alert to Hidden Dangers
Underground mining environments can quickly become hazardous with the accumulation of invisible gases like methane, which is highly explosive, and carbon monoxide, which can cause suffocation. Continuous gas monitoring is essential to safeguard workers against these dangers.
Portable gas detectors and fixed monitoring systems are widely used in mining operations. Portable detectors allow workers to check gas levels in specific areas, while fixed systems monitor entire sections of the mine. When gas levels approach unsafe thresholds, these systems trigger alarms, alerting workers to potential risks and enabling rapid evacuation if needed. This proactive approach helps mitigate one of the most significant threats to underground mining safety.
4. Regular Safety Drills: Preparing for EmergenciesEven with robust safety measures, incidents can occur, making preparation essential. Regular safety drills are a cornerstone of mine safety protocols, helping miners respond effectively to emergencies like fires, gas leaks, and rockfalls. These drills equip workers with crucial knowledge about evacuation routes, safe zones, and emergency procedures.
Mines often conduct specific types of drills, such as self-rescue device training, where miners learn to use equipment that provides breathable air in hazardous conditions. Additional drills for fire response and first aid ensure that all personnel are prepared to handle emergencies efficiently. By practising these scenarios, miners gain the confidence and skills needed to act quickly, reducing risks to themselves and their colleagues.
5. Vehicle Safety in Underground Mines: Minimizing Accidents with Technology
Mining vehicles are essential for transporting materials and equipment, but in confined underground spaces, they can pose risks if not properly managed. The use of automated safety systems in vehicles has become increasingly common in modern mines, helping to prevent accidents and improve operational efficiency.
Collision detection sensors and lane-keeping assistance technology help drivers navigate narrow tunnels and avoid potential collisions with walls or other vehicles. Some mines have also implemented remote operation technology, allowing workers to control vehicles from a safe distance, especially in high-risk zones. Routine vehicle inspections ensure that brakes, lights, and other essential systems are functioning correctly, further enhancing safety.
6. Access Point Safety: Securing Shafts, Declines, and Ramps
Access points, such as shafts, declines, and ramps, are critical infrastructure components that facilitate safe entry, exit, and material transport within the mine. Regular structural integrity checks ensure these pathways remain stable and functional, preventing incidents that could arise from weakened structures or erosion.
In addition, safety protocols and training are essential for workers using these access points. Workers receive training on safe procedures for entering and exiting shafts and are equipped with knowledge about emergency escape routes. This structured approach ensures that access points are not only secure but also well-managed in emergencies.
7. Embracing Predictive Maintenance and Condition Monitoring
To enhance safety and efficiency, many mining companies have adopted predictive maintenance technologies. These systems use sensors and data analytics to monitor the condition of equipment and infrastructure continuously. By tracking metrics like vibration, temperature, and wear, predictive maintenance can identify potential issues before they become problems, reducing the risk of unexpected breakdowns.
This technology allows for more precise scheduling of repairs, minimising downtime and ensuring that equipment is always in optimal working condition. It also reduces the need for miners to be in high-risk areas for extended periods, as maintenance can be done proactively based on data-driven insights.
Safety measures in above ground mining
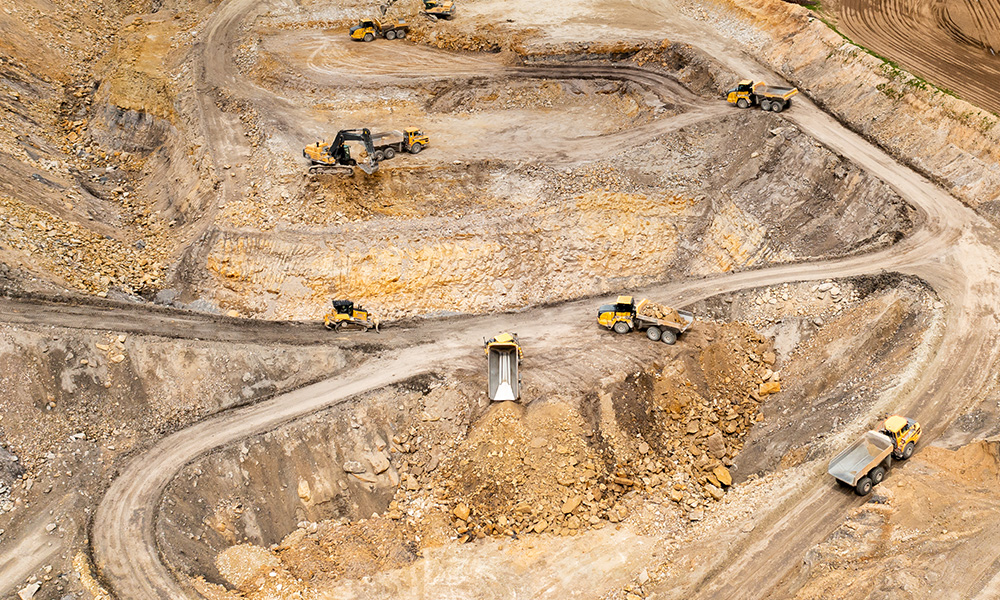
Above ground mining, also known as surface mining, involves the extraction of resources from open pits, strip mines, quarries, and mountaintops. While this type of mining eliminates the dangers of underground work, it comes with its own unique safety challenges, including large equipment hazards, high dust levels, and potential slope instability. Ensuring safety in surface mining requires comprehensive protocols, regular training, and the integration of advanced technology. Here are some key safety measures applied in above ground mining.
1. Slope Stability and Wall Monitoring
The walls and slopes in open-pit mines are vulnerable to collapse, particularly in steep sections. Maintaining slope stability is essential for preventing rockfalls and landslides that can endanger workers and equipment.
- Regular Inspections: Engineers and geologists regularly inspect pit walls and slopes for cracks or signs of instability.
- Slope Monitoring Systems: Modern mines employ radar, laser scanning, and ground-penetrating radar to monitor slope movement. These systems provide real-time data, alerting workers to potential collapses.
- Controlled Blasting: Blasting operations are carefully controlled to minimise vibration and reduce the likelihood of destabilising slopes.
2. Dust Control and Air Quality Management
Dust is a significant hazard in surface mining, as it can cause respiratory issues and reduced visibility, increasing the risk of accidents.
- Water Sprays and Dust Suppressants: Water sprays are commonly used to keep dust levels down on roads, loading areas, and crushers. Dust suppressants are also applied to areas with high dust levels to prevent airborne particles.
- Dust Extraction Systems: In areas where crushing and processing occur, dust extraction systems capture airborne particles, ensuring safer air quality.
- Respiratory Protection: Workers are provided with personal protective equipment (PPE), like dust masks and respirators, especially in high-dust areas.
3. Traffic and Vehicle Safety
Above ground mining involves the use of large, heavy machinery such as haul trucks, bulldozers, loaders, and excavators. Managing traffic flow and vehicle safety is crucial to prevent accidents.
- Defined Traffic Routes and Barriers: Roads within the mine site are carefully planned, with clear signage and barriers to separate vehicle and pedestrian traffic.
- Collision Avoidance Systems: Many mining vehicles are equipped with collision detection systems and proximity sensors that alert operators to obstacles or other vehicles.
- Driver Training and Fatigue Management: Operators receive regular training to maintain skills, and fatigue management programs monitor work hours to prevent drowsy driving.
4. Blast Safety and Controlled Detonations
Blasting is a common part of surface mining to break up rock for easier excavation, but it poses safety risks if not managed properly.
- Controlled Blasting Techniques: Blasts are precisely timed and controlled, often using electronic detonators, to reduce fly rock and vibration.
- Blasting Exclusion Zones: Areas surrounding the blast site are evacuated and monitored to keep personnel at a safe distance.
- Post-Blast Inspections: After a blast, the area is inspected for loose rock and debris before workers are allowed to enter, ensuring it is safe for re-entry.
5. Environmental Hazard Management
Surface mining can disrupt local ecosystems and create water and soil contamination risks, which require diligent management.
- Erosion and Runoff Control: Measures such as slope stabilisation, water drainage channels, and sediment control ponds help manage runoff and prevent soil erosion.
- Water Quality Monitoring: Regular water quality testing helps detect contaminants that could seep into nearby water sources. Mines use containment and treatment systems to prevent and treat runoff.
- Reclamation and Rehabilitation: After the mining site is no longer active, companies are often required to rehabilitate the land, restoring it for other uses and reducing environmental impacts.
6. Safety Training and Emergency Preparedness
Worker safety in surface mining is enhanced through thorough training programs and emergency response readiness.
- Safety Drills and Simulations: Regular drills prepare workers to handle situations like fires, equipment malfunctions, and rockslides. Emergency evacuation procedures are regularly rehearsed to ensure quick response times.
- First Aid Training: Workers are trained in basic first aid, with key staff certified in advanced first aid for rapid response to injuries.
- Communication Systems: Reliable communication channels, including two-way radios and emergency alert systems, allow workers to report hazards and receive assistance quickly.
7. Personal Protective Equipment (PPE)
PPE is essential in reducing the risk of injury in surface mining operations.
- Protective Gear: Workers are provided with helmets, safety goggles, ear protection, and gloves to protect against flying debris, loud machinery, and other hazards.
- High-Visibility Clothing: Reflective vests and clothing ensure that workers are easily visible to operators of large machinery, reducing the likelihood of accidents.
- Heat Stress Management: Above-ground miners work in direct sunlight, and in hot climates, heat stress is a significant concern. Access to shaded rest areas, hydration stations, and heat illness training is critical to prevent heat-related health issues.
8. Predictive Maintenance and Equipment Monitoring
Maintaining equipment is essential for minimising breakdowns and reducing safety risks associated with mechanical failures.
- Predictive Maintenance Programs: Mining companies use data analytics to predict when equipment may fail and schedule maintenance before issues arise.
- Condition Monitoring: Sensors on critical components like brakes, engines, and tyres monitor equipment health, alerting maintenance teams to potential problems.
- Regular Inspections: Daily checks ensure that machinery is in good working order, with an emphasis on critical systems like brakes, hydraulic systems, and electrical wiring.
Safety Measures in Workshop and Plant Maintenance
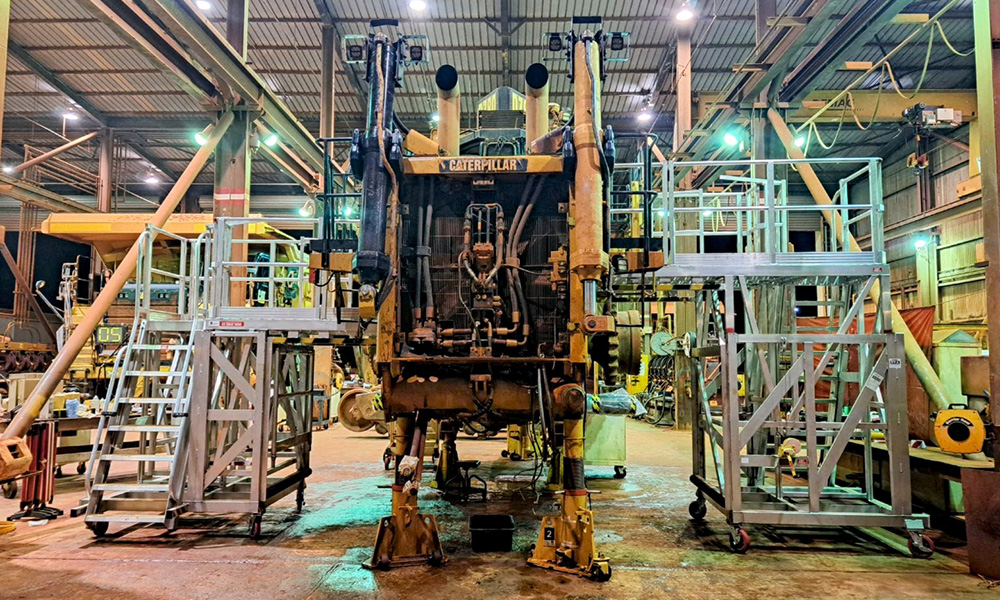
Workshop and plant maintenance are essential aspects of mining operations, where equipment reliability is critical to productivity and safety. Mining workshops involve repair and maintenance activities on heavy machinery, which pose unique hazards, including mechanical failures, exposure to high temperatures, chemicals, and heavy lifting. Here’s a look at key safety measures that ensure safe operations in these environments.
1. Machinery and Equipment Lockout/Tagout (LOTO)
- Purpose: LOTO procedures are essential in preventing accidental machine start-ups or energy release during maintenance.
- Process: Technicians disconnect the equipment from its power source and place a visible lock and tag on it, ensuring it cannot be reactivated until the repair is complete. LOTO procedures also include discharging any residual energy from the machinery to prevent accidents.
2. Personal Protective Equipment (PPE)
- Protective Gear: Maintenance workers are provided with specialised PPE, including gloves, goggles, helmets, and hearing protection, to shield against hazards like flying debris, loud machinery, and chemical exposure.
- Respirators and Masks: When working with dust, fumes, or chemicals, respirators are essential to protect against respiratory hazards.
- High-Visibility Clothing: In busy workshops or plant environments, high-visibility clothing helps workers stay visible to equipment operators, reducing the risk of accidents.
3. Ergonomic Safety and Proper Lifting Techniques
- Ergonomic Design: Workshops are designed with ergonomics in mind, providing tools and workstations that minimise strain on workers.
- Lifting Techniques and Training: Workers are trained on safe lifting techniques, especially when handling heavy or awkward components, to prevent musculoskeletal injuries.
- Lifting Aids and Equipment: Hoists, cranes, and forklifts are used for heavy lifting tasks, with strict protocols to ensure safe operation and load handling.
4. Fire Prevention and Hazardous Material Management
- Fire Safety: Workshops contain a variety of fire hazards, including flammable liquids and gases. Fire prevention measures include proper storage of flammable substances, fire suppression systems, and the availability of fire extinguishers.
- Hazardous Material Handling: Chemicals like lubricants, coolants, and solvents are handled according to Material Safety Data Sheets (MSDS), and staff receive training on proper usage, storage, and disposal to prevent spills and contamination.
5. Fall Protection Systems
- Personal Fall Arrest Systems (PFAS): Workers wear harnesses connected to secure anchor points via lanyards or lifelines, preventing falls from height. PFAS are crucial in areas without guardrails or stable platforms.
- Guardrails and Barriers: Permanent or temporary guardrails are used around elevated work areas to create physical barriers that prevent falls.
- Safety Nets: Nets positioned below the work area catch falling tools or materials, protecting workers and equipment below from injury and damage.
6. Elevated Work Platforms
- Scaffolding: Properly installed scaffolding provides a stable platform for workers to access elevated sections safely. Scaffolds are regularly inspected to ensure structural integrity and stability.
- Mobile Elevating Work Platforms (MEWPs): Equipment like scissor lifts and boom lifts allow workers to reach high or difficult areas. Workers receive training on MEWP operation, and platforms are equipped with guardrails and emergency controls.
- Aerial Lifts: Similar to MEWPs, aerial lifts like cherry pickers provide vertical and horizontal reach for accessing difficult locations. Safety protocols include wearing a harness and following the lift’s weight limit to prevent tip-overs.
7. Ladder Safety
- Fixed Ladders with Cages: Fixed ladders have built-in cages to protect workers as they ascend or descend. Some also include vertical lifelines for additional security.
- Extension and Step Ladders: When ladders are necessary, workers are trained in proper ladder setup, usage, and load limits to prevent slips or falls. Ladders should be stable, set on a level surface, and have anti-slip feet for added stability.
- Three-Point Contact Rule: Workers are trained to maintain three points of contact (two hands and one foot, or two feet and one hand) on the ladder at all times to minimise fall risk.
8. Access to Confined and Hard-to-Reach Areas
- Rope Access Systems: In cases where platforms or ladders cannot reach, certified rope access technicians use ropes, harnesses, and anchors to reach high or confined spaces safely. This technique requires extensive training and certification.
- Cranes and Hoists: Cranes or hoists can lift personnel baskets, allowing safe access to overhead or difficult-to-reach areas, provided the crane and basket meet safety standards.
- Telescopic Tools and Inspection Cameras: For inspection and light maintenance tasks in confined spaces, telescopic tools or remote cameras are used to minimise the need for physical entry, improving safety in tight or hazardous environments.
9. Permit to Work (PTW) Systems
- Permit Requirement for High-Risk Access: Access to heights or confined areas often requires a PTW, which ensures that all necessary safety protocols are in place. The permit process includes hazard assessments, PPE checks, and identification of rescue equipment.
- Rescue Plans and Emergency Protocols: Workers must have clear rescue plans for accessing heights or confined spaces. Rescue equipment, such as pulleys, rope systems, or emergency descent devices, is on-site to facilitate safe evacuation in an emergency.
10. Fall Prevention and Rescue Training
- Fall Prevention Training: Workers receive training on fall hazards, fall protection equipment, and the correct use of platforms, ladders, and harnesses. This training includes identifying hazards and inspecting equipment before use.
- Rescue and Evacuation Drills: Regularly conducted drills prepare workers and supervisors for emergency rescues from heights or confined spaces. Rescue plans are reviewed frequently to ensure preparedness.
11. Personal Protective Equipment (PPE) for Height Work
- Harnesses and Shock-Absorbing Lanyards: Workers use full-body harnesses with shock-absorbing lanyards that reduce the force of a fall. Self-retracting lifelines add mobility while maintaining fall protection.
- Non-Slip Boots and Gloves: High-grip boots prevent slips on platforms and ladders, and gloves improve grip while handling tools or climbing.
- Tool Lanyards: Tools are attached to lanyards to prevent them from falling and causing injury to workers below.
Safety Innovations and Advancements in the Mining Industry
Many Australian and global mines are integrating advanced safety technologies, such as autonomous vehicles, remote monitoring, and wearable safety devices, to reduce worker exposure to hazardous conditions. Examples include real-time location tracking, ventilation monitoring, and collision avoidance systems.
- Drones and Robotics: Used for inspections and monitoring, reducing human exposure to hazardous environments.
- Anglo American Australia uses remote dozer operations at the Bowen Basin Mine.
- RioTinto regularly uses robotics for transport automation dubbed AutoHaul™ and drones for surveying high walls and 3D mapping,
- Real-Time Data Analytics: Enhances predictive maintenance and risk assessments, enabling proactive safety measures.
- BHP’s Integrated Remote Operations Center (IROC) reached its 10-year celebration of remote monitoring and predictive maintenance.
- Wearable Sensors: Sensors embedded in harnesses or helmets can detect sudden movements or drops and alert supervisors to potential falls, enhancing worker safety in real time.
- Wenco’s Smart Caps embedded with fatigue sensors for haul truck operators. These caps monitor brainwaves and detect signs of fatigue, alerting operators and supervisors to potential drowsiness.
- Smart bracelets and exoskeletons are entering the mines to aid in automation and safety regulations.
- Artificial Intelligence: Mining companies are increasingly leveraging AI to improve exploration, safety, and efficiency:
- Barrick Gold partnered with Fleet Space Technologies to use satellite and seismic AI-driven mapping at Reko Diq in Pakistan, speeding up copper exploration while minimising environmental impact.
- Almonty Industries introduced AI-powered safety at its South Korean tungsten mine through wearable tech that tracks biometrics and location, allowing proactive responses to miner fatigue and emergencies.
- Fortescue and Liebherr are developing the world’s first autonomous, zero-emission haulage system for mining trucks in Australia, supporting Fortescue’s net-zero goals and optimising fleet performance.
Thanks for Reading Our Mining Guide
In exploring the varied types of mining—surface, underground, underwater, and maintenance services—we see a snapshot of an industry that’s not only vital to Australia’s economy but essential to countless global industries. From the excavation of iron ore and coal to the extraction of precious metals, mining fuels key sectors and supports technological advancements that shape our daily lives.
The mining industry’s success hinges on robust services and maintenance practices. Planned shutdowns and emergency repairs ensure the machinery that drives extraction runs smoothly, safely, and efficiently. In this way, maintenance isn’t merely operational; it’s a strategic component that minimises downtime, maximises productivity, and ultimately safeguards the well-being of those on-site.
As we look toward the future of mining in Australia, safety and sustainability will continue to lead the way, with new technologies like predictive maintenance, remote monitoring, and automation setting new standards for safety and efficiency. The Australian mining sector, with its pioneering safety measures and commitment to innovation, stands as a model for mining operations worldwide.