A Comprehensive Guide
Underground Mining is a major mining industry in Australia, and mine operators across the country have refined the science of extracting minerals from beneath the earth’s surface. It’s a complex process involving various techniques and Underground Mining Equipment designed to reach, extract, and transport valuable minerals efficiently and safely.
This guide explores in depth the various methods and equipment used in underground mining, with a focus on safety, efficiency, and adherence to industry standards.
SafeSmart Access’ Role in Underground Mining
SafeSmart Access has become the go-to provider for height access solutions in the mining industry. Known for engineering custom solutions that put safety and compliance front and center, SafeSmart meets the growing demand for reliable, adaptable access equipment tailored to the unique challenges of mining.
For a closer look at SafeSmart’s impact on mining operations, check out their real-world success stories in these case studies. For a complete list of access solutions, visit our Underground Mining Solutions page for products and examples of mine safety success. Visit our Mining overview page for a quick snapshot of who we’ve worked with and our solutions.
Accessing the Ore Body
In underground mining, reaching the ore body isn’t just any old step—it’s the big one. This crucial phase is where everything kicks off, setting up the pathways and access points that miners will rely on to safely extract the hidden ore and minerals deep below. Depending on factors like how deep the ore is, its shape, and what kind of rock is around it, mining teams choose different methods to get down there.
Each approach goes beyond functionality; it’s a feat of engineering. Surveyed, analysed, and built to handle the massive pressures of the earth and the weight of heavy machinery rumbling above each shaft, adit, and ramp.
1. Shafts
Shafts are vertical or near-vertical tunnels used for transporting personnel, equipment, and materials, as well as hoisting ore to the surface. They are essential for providing access to different levels of the mine and are constructed using two primary methods:
- Drilling and Blasting: This traditional method involves using explosives to create the shaft. It is a well-established technique that has been used for many years in mining operations.
- Raise Boring: This method involves drilling a pilot hole from underground to the surface and then reaming to enlarge the hole. It offers a more controlled and precise way of creating shafts.
Shafts are categorised based on their specific functions:
- Production Shafts: These are dedicated to hoisting ore to the surface, playing a crucial role in the transportation of extracted minerals.
- Service Shafts: These are used for the transportation of personnel, equipment, and materials within the mine, contributing to the overall logistics of the operation.
2. Declines (Ramps)
Declines, or ramps, are inclined tunnels that grant access to multiple levels within the mine, making them a crucial element of underground infrastructure. These tunnels allow vehicles to drive directly to various sections, streamlining the movement of ore using trucks and other transport machinery. Depending on the layout of the mine and the positioning of the ore body, the decline design may be constructed in a spiral around the deposit or follow a more straightforward, linear path.
This flexibility in decline mining enables efficient access to different areas, adapting as mining progresses deeper or spreads horizontally. The versatility of the ramps and crosscuts makes them indispensable, as they can be adjusted to match evolving operational needs, supporting the safe and effective extraction of resources.
3. Adits
Adits are horizontal tunnels that serve as entry points into the mine, typically extending from the side of a hill or mountain. These are often called portals or portal entrances. They provide a direct pathway to reach shallow ore bodies without the complexity and expense of sinking deep shafts, making them a more straightforward option for accessing minerals near the surface.
Adits are particularly useful in terrains where the ore body is exposed or close to the surface along a slope, allowing easy access with minimal excavation. In addition to their practicality, adits often enhance ventilation within the mine, as fresh air can flow more freely through these horizontal openings, supporting both safety and operational efficiency.
Underground Mining Industry Methods
After establishing access to the ore body, a range of mining methods can be utilised to extract the valuable minerals within. Each technique offers distinct features, applications, and challenges specifically tailored to suit the type, shape, and location of the ore body, as well as the surrounding geological conditions.
The methods we’ll go through below are selected not only for their effectiveness in reaching the ore but also for their safety, cost-efficiency, and environmental considerations.
1. Room and Pillar (Bord and Pillar) Mining
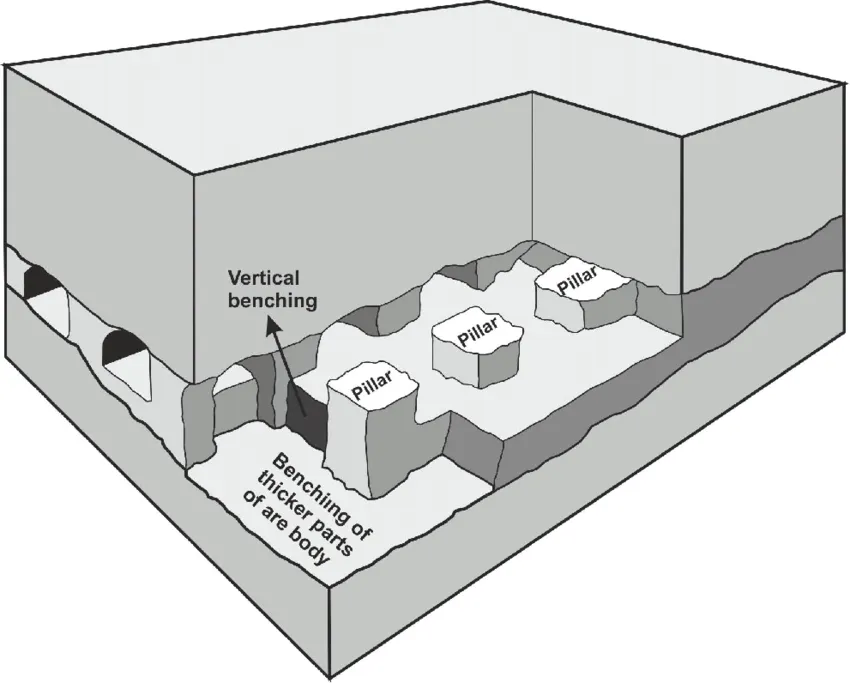
Room and pillar mining is a bit like carving out a checkerboard underground. It’s a method that’s been widely used for flat-lying deposits—coal, potash, and salt. These minerals tend to spread out in horizontal layers, making them perfect for this kind of approach.
This method shines for flat deposits like coal, potash, and salt. Since these minerals are layered out flat, room and pillar is an efficient, practical choice.
How It Works:
- Development – The first phase is all about setting up the layout. Miners drive entries and crosscuts, “drifts”, to create a grid across the deposit, like setting up the foundation of a neighbourhood. These entries don’t just provide access; they’re carefully planned to support the mine structurally, creating a network of paths that hold everything together. Roadheader machinery can be used in this process.
- Extraction – Once the grid is in place, the team starts working on the “rooms”—the sections of ore between the pillars. Here’s where the real action happens, with miners carefully extracting the ore while leaving the support pillars intact to hold up the roof and keep things stable. Various types of continuous miner machinery are used in this process.
- Retreat Mining (Optional) – This is where things get tricky, and it’s not for the faint-hearted. In this higher-risk phase, miners go back to pull out the remaining pillars, causing a controlled collapse of the area as the ore is removed. It’s a trade-off: retreat mining maximises ore recovery, but it does raise the risk of roof collapse, so safety measures are ramped up to keep everyone protected. Breaker Line Support vehicles are often used during this process.
Room and pillar mining is relatively simple to set up and doesn’t require as much upfront investment as more complicated mining methods. Plus, its modular approach lets operators adapt on the go, giving them flexibility in managing the mine.
This method does have its limitations. You can’t take out all the ore because those support pillars have to stay largely intact to keep the roof from caving in, which means some ore gets left behind. If retreat mining is on the table, it brings added risks, with the chance of roof collapse as pillars are removed. This phase requires careful planning, constant monitoring, and top-notch safety practices to minimise risks.
2. Cut and Fill mining
Cut and fill mining is a method where miners work from the bottom up, taking out the ore in horizontal slices and filling in the gaps as they go. Using an obscure metaphor with cake, you can picture this as carefully removing layers of cake and then filling in each layer with frosting to keep the whole thing from collapsing. This method is great for ore bodies that are steeply slanted, oddly shaped, or located in areas where the surrounding rock is fragile and needs extra support.
This technique is ideal for steep or irregular ore bodies and areas where the rock is too weak to stand on its own. If the geology is tricky or unpredictable, cut-and-fill mining is often the best choice.
How It Works:
- Cutting – Miners start at the bottom and work their way up, drilling and blasting each horizontal slice of ore. By removing the ore layer by layer, they keep things stable and have better access to each section as they go. This “bottom-up” approach means they can support the ore body effectively, making it a safer and more controlled operation.
- Filling – After each slice is mined, the empty space (or “void”) is filled with waste rock or tailings, which are by-products of mining, sometimes mixed with cement for extra support. This backfilling helps stabilise the surrounding rock, reducing the risk of collapse and providing a solid foundation for the next layer. It’s all about creating a safer environment and adding stability with every step.
Cut and fill mining allows for high recovery rates since miners can take out more ore than they might with other methods. The backfill not only supports the rock but also makes the environment safer, which is especially crucial when working in weaker or unstable rock formations.
This method does come with a few trade-offs. Because each layer has to be filled in right after it’s mined, the operating costs are higher, and production tends to be a bit slower compared to other methods. The process requires careful planning and attention to detail, so it’s a more labour-intensive and time-consuming approach. But for those tricky, challenging ore bodies, cut-and-fill Mining offers a balanced approach that emphasises stability and thorough ore recovery.
3. Longwall Mining
At its core, longwall mining involves cutting through a long “wall” of ore and slicing out the material in one consistent sweep. This approach works best in extensive, consistent ore bodies, like wide seams of coal that run deep beneath the earth, where the ore’s uniformity makes it possible to maintain a steady extraction rhythm.
The machinery involved is referred to as an Armoured Face Conveyor or AFC, and if you haven’t seen it, it’s difficult to describe just in words. It’s like a rock carving mandolin capable of supporting the ore roof structure and transporting the sheared ore elsewhere. We’ve attached some images below to get an idea of how this bit of longwall machinery works.
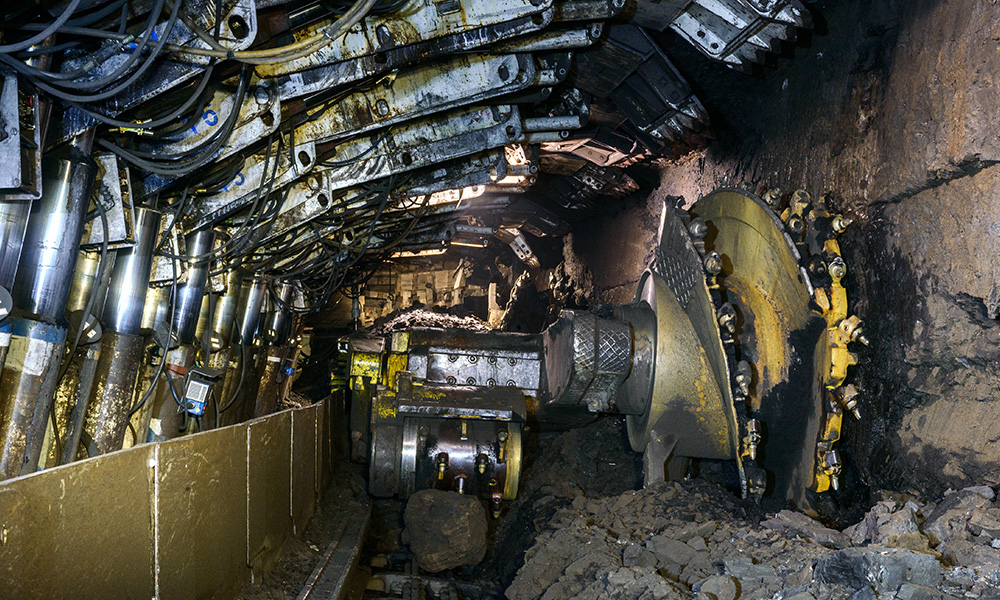
How It Works:
- Setting Up the Infrastructure: The first step in longwall mining is all about prep. Hydraulic roof supports are installed along the wall to hold everything in place. These supports prevent any untimely roof collapses while mining is underway. A conveyor system is also positioned to whisk away the extracted material, and an automated shearer—a powerful cutting machine—gets ready to work its way across the ore face.
- Extraction: Once everything’s ready, the real action begins. The shearer moves back and forth along the ore face, carving out chunks of coal in a steady, relentless rhythm. It’s a highly coordinated process: as the shearer slices through the ore, the hydraulic supports advance with it, ensuring the roof stays intact above the work area. Behind the supports, the roof is left to collapse in a controlled way into a “goaf” (a mined-out area).
- Transport: Once on the conveyor, the ore will take a series of conveyors from the longwall miner to what is called a beam stage loader and then further onto various conveyors or vehicles. For sweeping or drifting tunnels, flexible conveyor trains can be used to move the material throughout the mine.
This method stands out for its speed and efficiency. With continuous cutting, production rates soar, allowing miners to pull vast quantities of ore in a relatively short time. And it’s not just about speed—longwall mining maximises resource recovery, leaving minimal ore behind.
Longwall mining isn’t without its challenges. The equipment and setup required for this method are expensive. Companies face enormous investments in hydraulic supports and conveyor systems. While the controlled roof collapse is part of the design, it can lead to surface subsidence—a phenomenon where the ground above the mined-out area dips or sinks. This subsidence can have knock-on effects on the environment and infrastructure above ground, which means mine operators need to weigh these risks against the benefits.
4. Block Caving
BlCavingving is one of those “go big or go home” mining methods. It’s all about working with gravity to break down massive sections of ore with minimal direct effort. By strategically weakening part of the ore body—what is called “undercutting”—miners set off a natural chain reaction that causes the overlying material to collapse. This caving effect breaks up the ore, which then tumbles down to collection points where it’s ready to be transported to the surface. It’s a highly efficient, gravity-driven technique, perfect for handling vast, low-grade deposits like copper and diamond.
This method shines with large-scale, low-grade ore bodies that are spread out and relatively uniform. For deposits like copper and diamonds, block caving makes the most sense when you need to extract huge volumes efficiently.
How It Works:
- Undercutting – The process kicks off with the creation of a void, or undercut, right below the ore body. This “undercut” isn’t just any space; it’s a strategically placed gap that destabilises the entire ore section above, making it ripe for caving.
- CCaving– Once the undercut is in place, gravity takes over. The weakened ore body fractures and collapses under its own weight, and the broken ore falls into special collection points called draw points. From there, it can be loaded up and hauled to the surface for processing. This process keeps going, creating a self-sustaining flow of ore that can be collected continuously, allowing miners to extract vast quantities over time without additional blasting.
Block caving is cost-effective, especially when you’re dealing with low-grade ore. By letting gravity do most of the heavy lifting, this method offers a low cost per tonne, which is a big deal for large operations. The high production rate is ideal for massive deposits, making it possible to process a lot of more efficiently.
Of course, there’s a catch. Block caving requires a hefty initial investment to set up the undercut and drawpoints, as well as meticulous planning to make sure the whole system holds up under pressure. Plus, the caving process can lead to ground subsidence—essentially causing the surface above to sink or shift. This poses environmental challenges, and it means that nearby landscapes and infrastructure need to be monitored and managed to minimise any potential impacts.
5. Sublevel Stoping

Sublevel stoping is all about working smarter, not harder, by creating multiple layers, or “sublevels,” within an ore body. From each of these sublevels, miners can drill and blast their way through the ore, breaking it up in a controlled way that makes extraction safer and more efficient. It’s an ideal approach for ore bodies that are steeply angled and surrounded by strong, stable rock that can handle the blast and stay intact even as sections are mined out.
This method works well with steeply dipping ore bodies where the rock around the ore is solid enough to withstand the blasting and the resulting empty spaces.
How It Works:
- Development – The first step is to set up a series of sublevels throughout the ore body. These sublevels are connected by access tunnels, or “drifts,” that allow miners to move easily through the area. By creating these levels, miners can access the ore body section by section, ensuring a smooth workflow and better control over the mining process.
- Production – Once the sublevels are in place, it’s time for drilling and blasting. Long holes are drilled from each sublevel into the ore, and then blasting breaks up the ore into smaller, manageable pieces. The broken ore falls into a muck pile, where it’s ready to be scooped up and transported to the surface for processing. This process is efficient and can be repeated at each sublevel, allowing for continuous production without constant setup.
Sublevel stoping is a highly productive method, and because it’s well-suited to mechanisation, large-scale equipment can be used to speed up the extraction process and improve safety. Automation can also play a role, making it easier for miners to work with precision and reducing the need for direct human involvement in risky areas.
This method requires stable ground conditions—if the rock isn’t strong enough, there’s a risk of collapse. Careful planning is also essential to prevent ore dilution, where waste rock mixes with the ore, lowering its quality. The layout and sequence of each sublevel need to be precisely designed to keep both the miners and the ore quality safe.
Infrastructure and Support Systems
Getting to the ore body and extracting minerals is only part of the underground mining picture. To keep the whole operation safe and efficient, a range of infrastructure and support systems is needed. One of the most critical of these systems is ventilation.
1. Ventilation
Ventilation in a mine is essential. Without proper ventilation, conditions can quickly become unsafe, making it impossible for miners to work comfortably and securely. A well-designed ventilation system keeps the air fresh, controls dust, and maintains safe temperatures, ensuring a healthier environment underground.
Key Components of Mine Ventilation:
- Main Fans: These are the heavy-duty fans located on the surface that handle the big job of pushing or pulling air through the entire mine. They’re the main driving force that pumps fresh air into the mine’s intake airways and extracts stale air through the return airways, keeping the air cycle flowing consistently.
- Auxiliary Fans: In specific areas of the mine, auxiliary fans provide an extra boost of airflow. These are especially helpful in parts of the mine that are farther from the main air routes or require additional circulation to keep the air fresh. Think of them as the fans in hard-to-reach corners, making sure there’s good ventilation everywhere it’s needed.
- Airways: The ventilation system operates through a network of intake and return airways, which manage the direction and flow of air within the mine. Intake airways bring fresh air to active mining zones, while return airways carry used air, gases, and dust back to the surface. It’s like a continuous loop that keeps the air clean and moving.
- Ventilation Control Devices: Throughout the mine, there are various devices to control and direct airflow, including regulators, doors, and stoppings. These devices act as traffic signals for air, allowing mine operators to guide fresh air exactly where it’s needed and block off unused sections to prevent air stagnation. This way, the ventilation is precisely managed, keeping conditions safe and ensuring every working area gets the fresh air it needs.
- Gas Monitoring: Continuous gas monitoring systems are integral to modern ventilation. These sensors detect and measure concentrations of hazardous gases, such as methane, carbon monoxide, and oxygen levels, alerting workers to dangerous conditions. Automated alarms and ventilation adjustments based on gas levels help maintain safety by preventing explosions, fires, and health risks associated with toxic gas exposure.
2. Ground Support
Ground support systems are essential for keeping everything stable and secure. These systems are designed to reinforce rock walls and prevent collapses, making sure mining crews can work safely and equipment stays protected. Implementing the right support system depends on the unique geology of the mine, the size of the tunnels or openings, and the stability of the surrounding rock.
Key Ground Support Methods:
- Rock Bolts and Cable Bolts: These are like anchors for the rock. Rock bolts and cable bolts are inserted into drilled holes in unstable rock layers, holding them firmly in place and providing immediate support. Bolting is often undertaken by Rock Bolter Machinery, which is capable of drilling and bolting together.
Cable bolts are generally used in deeper, larger spaces where stronger support is needed. They offer flexibility and can handle heavier loads, which is perfect for bigger openings in the mine. - Shotcrete: Shotcrete is essentially concrete that’s sprayed onto rock surfaces, creating a quick, stabilising layer. As soon as new rock is exposed, shotcrete is applied to help prevent rock falls and reinforce larger open areas. It’s a fast and effective way to add extra stability right where it’s needed.
- Steel Sets and Mesh: In areas with larger openings or where rock needs more support, steel frames (called “steel sets”) and wire mesh are used. These are installed to add structural reinforcement, especially in tunnels or big caverns. Steel sets and mesh work together to spread out the load and stabilise the rock around larger voids, adding an extra layer of security.
- Monitoring Systems: Regular inspections and specialised monitoring tools—like extensometers, load cells, and strain gauges—are used to keep a close eye on ground movement. These instruments detect shifts in rock stability early on, allowing for timely interventions that enhance safety and prevent potential hazards before they become serious.
Each of these ground support methods is chosen to match the mine’s specific conditions, forming a proactive approach to maintaining stability and safety in the long run. With the right systems in place, miners can work with confidence, knowing that the rock around them is secure.
3. Machinery & Transportation
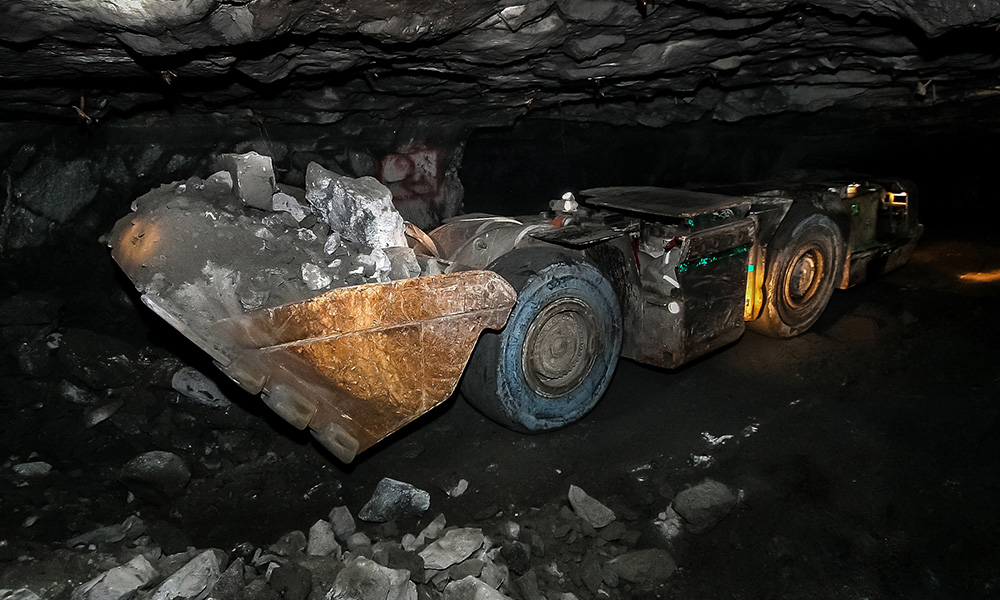
Efficient machinery and transportation systems are essential in mining operations for ore extraction, handling, and personnel movement. These tools make it possible to extract and move more efficiently while keeping miners safe and operations running smoothly. Each piece of equipment is chosen to fit the mining method, ore type, and depth, creating a system that’s both seamless and safe for everyone underground. Often, modern underground mining equipment is a lot shorter in height for obvious reasons, while also being shorter and sometimes electrified.
Key Mining Machinery:
- Longwall Mining Equipment: In longwall mining, a set of specialised machines work together to extract ore continuously along a wide face. Here’s how they work:
- Shield Supports: These hydraulic supports move forward with the shearer to hold up the roof and prevent collapses as mining progresses.
- Shearer: This is the main cutting machine that travels along the ore face, slicing off material continuously.
- Armoured Face Conveyor (AFC): Once the ore is cut, the AFC carries it along the face, moving it to the next stage.
- Beam Stage Loader (BSL): The BSL takes ore from the AFC and loads it onto crushers or conveyor belts, setting it up for transport out of the mine.
- Crusher: This machine breaks down large chunks of ore into smaller, more manageable pieces for easy movement along conveyors.
Ore Handling Systems:
- Load-Haul-Dump Machines (LHDs): LHDs are the workhorses of ore transport within the mine. These machines scoop up ore and carry it short distances, often from the mining face to crushers or ore passes. Haul trucks and LHD loaders fit under this group of ore-handling machines.
- Rail Systems: When ore needs to travel longer distances, rail systems step in. Locomotives and ore cars can carry heavy loads, making them reliable for moving bulk material efficiently through the mine.
- Conveyors: Continuous conveyor systems keep ore moving non-stop, taking it from extraction points to processing areas or storage without delays. Conveyors are ideal for direct, steady movement over long distances. Vertical conveyors throughout the shafts are also utilised to get material to the surface.
- Lifts and Skip Hoists: Lifts provide safe, efficient movement for workers and light gear, especially during shift changes. Skip hoists, or cage hoists, handle the heavy lifting, transporting large ore volumes from deep within the mine to the surface for processing. Both systems ensure seamless, safe, and efficient mine operation.
- Ore Passes and Chutes: These gravity-fed systems help ore move vertically within the mine. Ore has dropped down passes and funnelled through chutes, reducing the need for machinery to carry material up or down short distances.
Personnel Transport:
- Mantrips and Shuttle Cars: These vehicles or rail systems are designed to transport workers safely and efficiently to different areas in the mine. It’s like an underground shuttle service for the team.
- Cages and Skips: For vertical movement in mine shafts, cages and skips are essential. Cages transport miners and equipment, while skips are used to haul ore up to the surface.
Each of these components plays a vital role in keeping mining operations smooth and safe. Together, they create an optimised system for moving ore and personnel efficiently across different areas and levels within the mine, ensuring that everything from extraction to transport flows seamlessly.
4. Underground Workshops
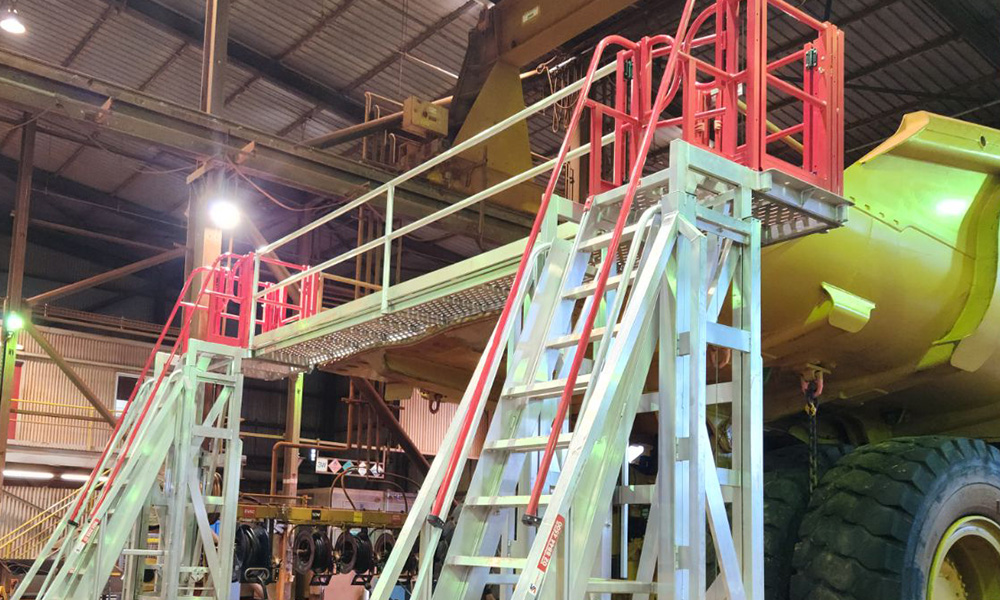
Underground workshops are essential facilities within a mine, providing a dedicated space for the maintenance and repair of machinery and equipment. These workshops reduce downtime, improve operational efficiency, and ensure that essential equipment is always ready for use. By situating workshops underground, mines can avoid the time and resources needed to transport equipment to the surface for repairs, allowing for immediate service and minimal disruption to operations.
Features:
- Maintenance Bays: Equipped with specialised tools and machinery, maintenance bays allow mechanics and technicians to perform regular servicing, troubleshooting, and repairs on mining equipment such as loaders, drills, and haul trucks. Access stands or work platforms are used here regularly.
- Storage Areas: Workshops include secure storage for spare parts, tools, lubricants, and other essential supplies. This ensures that necessary items are readily available, reducing delays and improving turnaround times on repairs.
- Electrical and Hydraulic Repair Stations: These stations support the complex repairs needed for mining machinery, particularly for systems like hydraulics and electrical components, which are critical to equipment performance and reliability.
- Fuel and Lubrication Stations: Underground workshops often include fuel and lubrication areas where equipment can be refueled and lubricated, minimising the need for trips to the surface and ensuring continuous operation.
- Safety Systems: Ventilation systems, dust and fume extraction, and fire suppression equipment are installed within workshops to maintain a safe environment, given that these facilities handle fuel, lubricants, and other potentially hazardous materials. Additionally, workshops have emergency exits and first-aid kits to address any incidents promptly.
Underground workshops offer several key advantages in mining operations. By allowing equipment repairs and maintenance to be completed on-site, they reduce downtime and keep machinery in service, minimising production delays. Proximity to work areas increases efficiency by saving time and energy that would otherwise be spent transporting equipment to the surface. Additionally, regular maintenance helps prevent breakdowns and extends equipment lifespan, ensuring it remains in optimal condition.
However, underground workshops also present challenges. They require enhanced ventilation to manage exhaust, fumes, and dust, as well as careful planning to address space constraints and accommodate large equipment. Strict safety measures are also essential, as hazardous materials like fuel and lubricants must be managed to prevent fire hazards and ensure compliance with regulatory standards.
5. Water Management
Effective water management is essential in mining, helping prevent flooding, control groundwater, and maintain safe working conditions. With systems like dewatering, water control, and, in certain cases, ground freezing, mines can manage water infiltration and keep everything stable in active zones.
Dewatering Systems:
- Pumps: High-capacity pumps are the go-to for removing groundwater that seeps into the mine. Strategically placed throughout the mine, these pumps work to keep work areas dry by handling different water volumes and flow rates, ensuring that water doesn’t interfere with mining activities.
- Sumps: Located in the lower sections of the mine, sumps are collection spots for excess water. They capture any groundwater that flows in, preventing it from pooling in work areas. This setup helps manage water levels and makes it easier for the pumps to clear the water out efficiently.
Water Control Measures:
- Grouting: Grouting acts like a water sealant. By injecting a special material into cracks or porous zones in the rock, it effectively blocks water from entering important areas and adds stability to the surrounding rock.
- Drainage Tunnels: These tunnels redirect groundwater away from active mining zones, cutting down on the need for continuous pumping. Channelling water to designated drainage points helps keep water levels in check and reduces pressure on the mine’s support systems.
- Ground Freezing: When water inflow is particularly tricky, ground freezing can offer a solution. This method involves freezing the ground around the mining area, creating a temporary barrier that keeps groundwater from seeping in. By circulating a coolant through a series of boreholes, the surrounding rock and water are frozen, effectively sealing off pathways for water. Ground freezing is especially useful in areas where the rock is highly permeable or unstable and where other methods alone might not be enough.
Underwater Mining
Underwater mining is a specialised form of mining that involves the extraction of minerals from beneath the sea or lake bed. This unique method presents its own set of challenges and requires specialised equipment and techniques to operate effectively.
It’s a world of its own, and we have a dedicated article on underwater mining equipment to detail all that is entailed.
Where to Next? Shock and Ore!
Once the ore reaches the surface, its journey is far from over. Above ground, it hops onto a new set of equipment designed to handle its next steps. Curious about what happens from here? You can continue on the ore journey here.
But there’s more to it than just transport. The ore often goes through several key stages before it’s ready for its final use. This can include crushing and milling to break down the ore into smaller, more manageable pieces, smelting to separate the valuable metals, and then shipping—especially for raw materials like iron ore.
The mining industry is an incredible process of extracting minerals from the earth. Historically, mining has been dangerous and fraught with danger. Thankfully with the modern methods and modern Underground Mining Equipment listed above, the mining industry is safer than ever.